Beneficios
- Incrementar los ingresos económicos de la compañía mediante una mayor recuperación de mineral.
- Aumentar el «throughput» del proceso de generación de mineral
- Disminución de las fallas del equipamiento originados por el proceso de mezcla
- Disminución de la huella de carbono.
- Aumentar el tiempo del equipo de despacho para otras tareas
Objetivos
- Minimizar la varianza de la mezcla planificada
- Aumentar la eficiencia del proceso de carguío y transporte
- Hacer fácil el trabajo del equipo de despacho
- Visibilizar la ejecución del plan de mezcla más allá del equipo de Operaciones
Industrias
- Minería.
- Cemento.
- Movimiento de materiales.
¿Por qué es importante controlar la mezcla de materiales y su varianza?
El valor mineralógico de una mina radica en la cuidadosa composición de sus materiales. En esencia, esta mezcla determina los futuros ingresos de la compañía, por lo que es crucial maximizar la recuperación de minerales.
Es importante tener en cuenta que los procesos mineros no son instantáneos; no se trata simplemente de ajustar la velocidad de un molino. Por lo tanto, a medida que varían los objetivos de mezcla, se incrementan los niveles de ajustes en los componentes aguas abajo, incluyendo la energía y los productos químicos necesarios.
¿Como las mezclas de materiales son hechas hoy?
Las formas de mezclar materiales en el chancador primario pueden variar de mina a mina. El equipo de operaciones recibe las instrucciones del personal de la planta y ejecuta la mezcla de materiales. En muchas minas la mezcla es hecha en forma manual y apoyándose con las posiciones que entregan los sistemas de GPS; incluso en minas donde los mineros tienen sistemas de control de flotas de las grandes marcas.
Los problemas en la ejecución de la mezcla se pueden ver agravados por escenarios más complejos que se dan hoy en día. Escenarios como alimentación de mezclas hechas por la combinación de operaciones a tajo abierto y minas subterraneas. O minas que hoy tienen camiones convencionales y autónomos. Estas situaciones que tiempo atrás no estaban en la agenda, o son escenarios que empiezan a ser más frecuentes.
¿Por qué ocurre incluso teniendo tecnología de control de flotas (FMS) las minas hacen la mezcla en forma manual?
Básicamente los FMS y sus algoritmos fueron construidos para maximizar el movimiento de material y no tienen como objetivo la mezcla de materiales. Es por eso que quien haya usado los tradicionales FMS se habrá dado cuenta que es casi una tortura lograr la mezcla objetivo con esos sistemas.
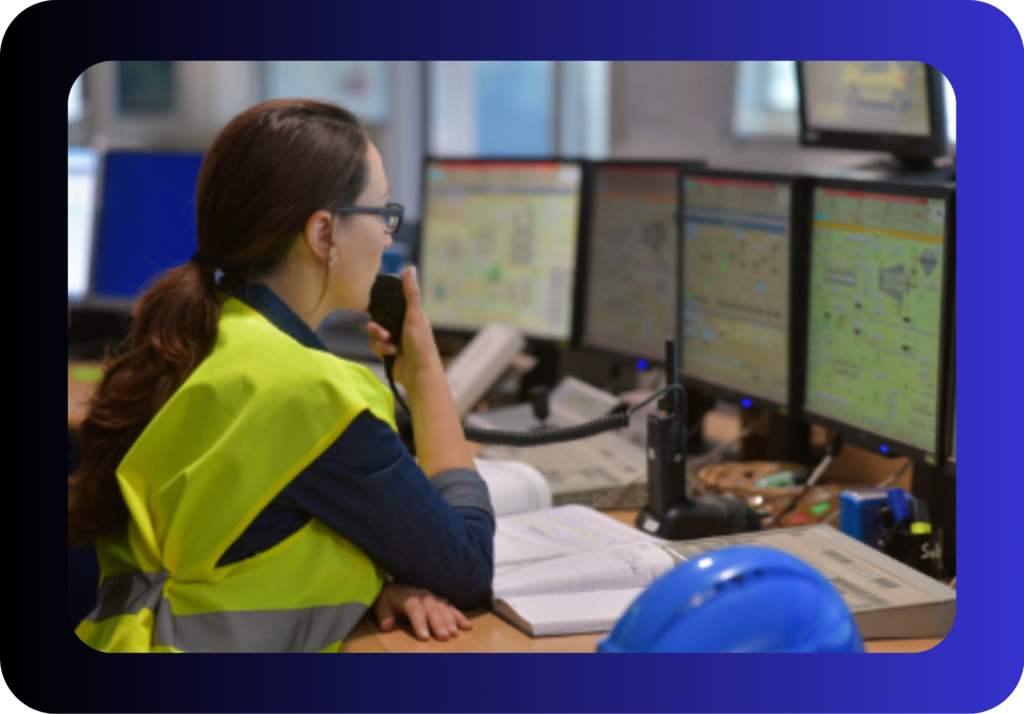
¿Cuáles son los problemas de hacer la mezcla en forma manual, o semi manual?
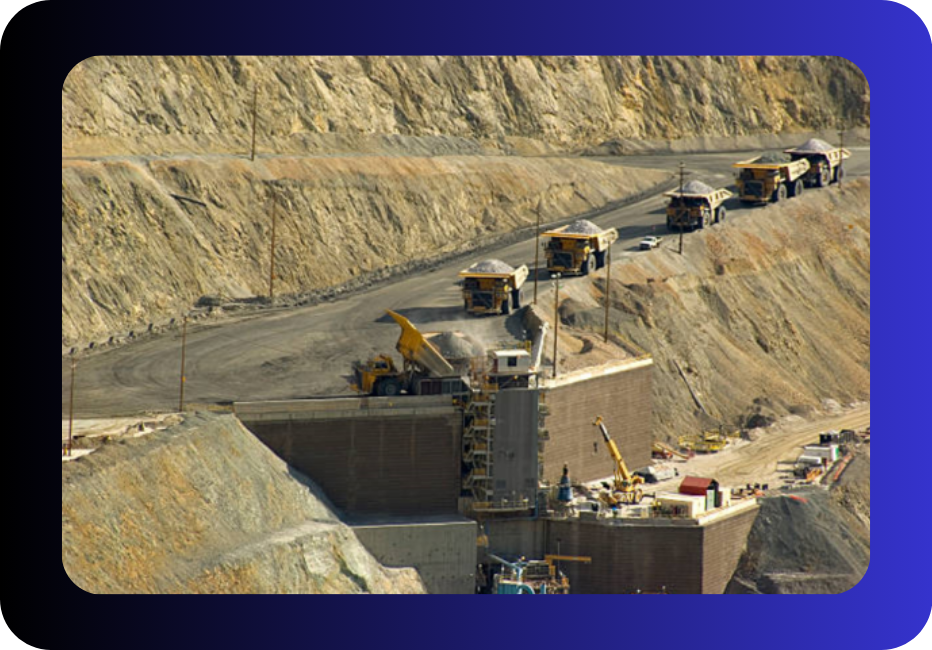
-
Aumento de los tiempos de colas de camiones
-
Aumento de la variación del proceso
-
Aumento de costos de químicos agua abajo
-
Disminuye el «throughput» final en la producción
-
Fallas en correas
-
Fallas en componentes de la molienda
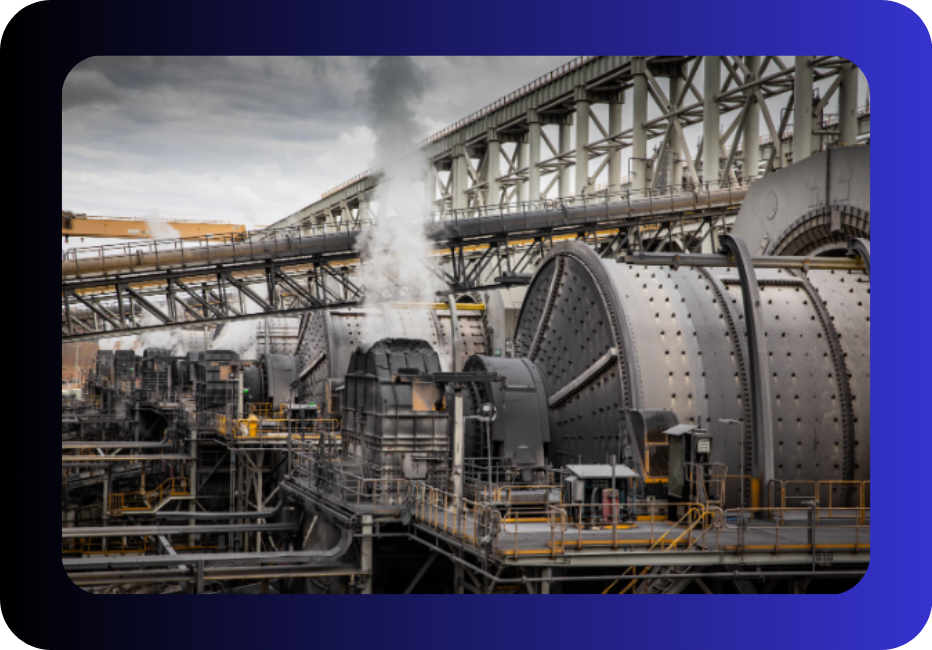
SOLUCIÓN:
Autonomous Material Blending Optimizer

La solución esta desarrollada como una infraestructura de optimización que permite adaptarse a como la mina opera y de esta manera ejecutar la mezcla planificada de mejor manera con un mínimo impacto sobre el manejo del cambio que las soluciones necesitan.

Construído con tecnología avanzada, permite a los usuarios configurar los parámetros de la mezcla objetivo en forma fácil y rápida. No importando los problemas que la operación tiene para ejecutar sus mezclas el sistema se diseña para que la interfaz de usuario sea fácil de operar por el personal.

El SW de optimización permite controlar diferentes escenarios de ejecución de la mezcla que van desde controlar una o más mezclas simultáneas, alimentadas por camiones y/o cargadores/palas. Entonces el software permite generar asignaciones dinámicas de equipos basadas en disminuir la varianza de la mezcla objetivo y minimizar las esperas de los equipos.

El software ha sido desarrollado para minimizar las actividades de manejo del cambio. Con este objetivo el software permite a sus usuarios lograr rápidamente los retornos de inversión.

Probado industrialmente.

Basado en nuevas infraestructuras de optimización, permite generar nuevas funciones objetivos y resolver problemas complejos de optimización.
Características de la solución
- Función objetivo customizable
- Facil de configurar
- Algoritmos Inteligentes
- Escalable a otras optimizaciones
- Integrable a los sistemas existentes de control de flotas.
- Transparente para los operadores de camiones
Preguntas frecuentes
El sistema puede manejar múltiples situaciones operacionales de como la mezcla es ejecutada por el equipo de operaciones. Los escenarios son:
- Carguíos que cargan camiones y los camiones transportan el material hasta el chancado.
- Mezcla para un chancador o dos chancadores, con un mismo objetivo mezcla.
- Mezclas de dos chancadores con mezclas objetivos diferentes.
- Mezcla hecha por un cargador que se mueve entre materiales a mezclar.
- Mezclas hechas por cargadores, tramming. (Roadmap)
Si tienes algún escenario contáctanos.
Si la mina posee un sistema de Flotas, y el sistema de flotas ya posee una pantalla en la cabina, nosotros nos integramos y así las asignaciones generadas por el optimizar son transmitidas a la cabina. Para los operadores, el sistema es transparente.
La configuración demora segundos, después de ya configurado el sistema empieza a trabajar en forma automática.
El optimizador tiene una visión agnóstica y la infraestructura de optimización permite integrar diferentes sistemas de control de flotas en forma simultánea. Se podría dar el caso que una mina opere con camiones propios y camiones contratistas, y cada empresa con su propio sistema por ejemplo.
La insfraestructura de optimización permite operar con diferentes procesos de extracción. Por lo tanto la integración de dos procesos diferentes no es un impedimento para manejar el proceso de mezcla de una mina con dos procesos diferentes.
No, la solución es adaptable para casos de negocios que requieren la combinacion de materiales con diferentes caracteristicas. Por ejemplo, la industria cementera tiene procesos de mezclas que requieren tecnologías que permitan asegurar la calidad del producto final.
Sí, la infraestructura de optimización permite modelar el proceso de mezcla de cada mina por forma separada. Es decir, la función objetivo puede ser «customizada» según sea la necesidad.
La solución permite manejar flujos de materiales más allá de los flujos de alimentación primaria. Por ejemplo, el optimizador puede manejar los flujos a botaderos de estéril o stockpiles.
¡Estaremos contestando tu mensaje a la brevedad!